The Impact of Precise Injection Moulding in Metal Fabrication
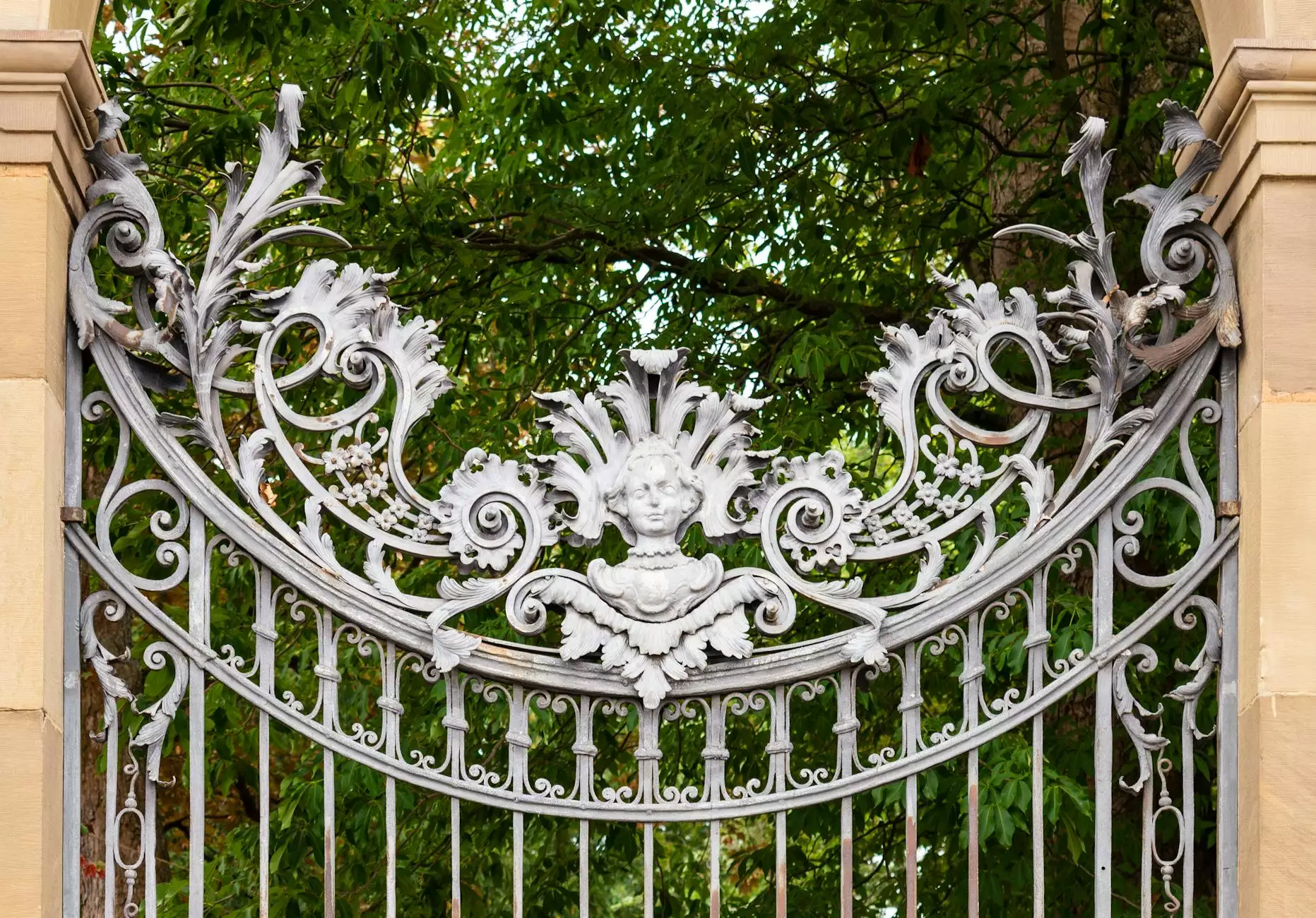
In the realm of metal fabrication, precision and efficiency are paramount. One of the leading technologies that has revolutionized this industry is precise injection moulding. This technique not only enhances production quality but also optimizes manufacturing processes, making it a cornerstone of modern fabrication techniques. In this article, we will delve into the intricate world of precise injection mould, exploring its advantages, applications, and the future of this pivotal manufacturing method.
What is Precise Injection Moulding?
Precise injection moulding is a manufacturing process that involves injecting molten material into a mould to create precise parts and components. Typically, thermoplastics and metals are used in the moulding process, allowing for complex designs and high-fidelity reproductions. The use of advanced technology in this method ensures that every produced part meets exact specifications, which is particularly important in industries where tolerances are critical, such as aerospace, automotive, and medical manufacturing.
Key Advantages of Using Precise Injection Moulding
The benefits of adopting precise injection moulding are manifold. Here are some of the key advantages:
- High Precision and Accuracy: The primary advantage of precise injection moulding lies in its ability to produce components with remarkable consistency and tight tolerances.
- Efficiency in Production: The process is highly efficient, allowing for the mass production of identical parts, significantly reducing lead times.
- Cost-Effectiveness: Once the mould is created, the cost per part decreases significantly, making it economical for large production runs.
- Design Flexibility: This manufacturing method allows for intricate designs that would be impossible or prohibitively expensive using other methods.
- Material Versatility: A wide range of materials can be used with injection moulding, including various plastics, metals, and composite materials.
The Role of Precise Injection Mould in Metal Fabrication
In the field of metal fabrication, the use of precise injection mould technology has grown tremendously. The ability to create complex geometries with high precision makes it invaluable in producing components such as:
- Auto Parts: Many automotive components require high precision to ensure vehicle safety and performance, making precise injection moulding a critical technique in this sector.
- Aerospace Components: The aerospace industry heavily relies on stringent tolerances and consistent quality, where precise injection moulding demonstrates its strength.
- Medical Devices: Devices used in the medical field necessitate reliability and safety, achieved through the meticulous process of precise injection moulding.
- Consumer Electronics: The production of compact and complex electronic components benefits greatly from the efficiency of injection moulding.
How Precisely Injection Moulding Works
The process of precise injection moulding involves several key steps:
- Mould Design: Engineers design the mould, considering the product specifications, material properties, and production volume.
- Mould Fabrication: The mould is then fabricated using high-strength materials that can withstand high pressures and temperatures.
- Injection of Material: Molten material is injected into the mould under high pressure, ensuring that it fills every cavity and detail.
- Cooling and Solidification: Once the mould is filled, it is cooled, allowing the material to solidify and take the shape of the mould.
- Mould Removal: The mould opens, and the finished part is ejected, ready for inspection and further processing.
Applications Across Industries
The versatility of precise injection mould extends to various industries, demonstrating its essential role in creating innovative solutions:
1. Aerospace
Aerospace manufacturers utilize precise injection moulding for producing lightweight yet sturdy components that are crucial for aircraft performance and safety.
2. Automotive
This sector benefits immensely from cost-effective mass production of parts such as dashboards, exterior and interior trims, and even engine components.
3. Medical
With stringent regulatory requirements, the medical industry relies on injection moulding to produce surgical instruments, housings for diagnostic machines, and more.
4. Electronics
The rapid production of casings and intricate components in consumer electronics showcases the adaptability and efficiency of injection moulding.
Choosing the Right Injection Moulding Partner
Finding a competent metal fabricator experienced in precise injection moulding is crucial for any business looking to leverage this technology. Here are some factors to consider when choosing a partner:
- Experience and Expertise: Check for a solid track record in industries relevant to your project.
- Technology and Equipment: Ensure they utilize modern machinery and best practices in mould design and production.
- Quality Control: An effective quality control system is essential to maintain consistency and avoid defects.
- Material Knowledge: A good partner will have extensive knowledge of various materials and their properties.
- Flexibility: Choose a partner who can adapt to your changing needs and project specifications.
The Future of Precise Injection Moulding
As technology evolves, so does the landscape of precise injection moulding. Emerging trends include:
- 3D Printing Integration: Combining traditional moulding with additive manufacturing techniques for enhanced design flexibility.
- Smart Manufacturing: Incorporating IoT and automation to streamline production processes and monitor quality in real-time.
- Sustainable Practices: A shift towards using eco-friendly materials and minimizing waste in the moulding process.
- Advanced Simulation: Leveraging simulation software to optimize mould design and reduce time in prototyping.
Conclusion
In conclusion, precise injection moulding stands as a pillar of modern metal fabrication, bridging the gap between design ambition and manufacturing reality. Its ability to produce high-precision components efficiently and cost-effectively makes it indispensable across a myriad of industries. Businesses seeking to enhance their manufacturing capabilities should consider adopting this transformative process to stay competitive and meet the demands of a rapidly changing market.
Understanding the intricacies of precise injection moulding will empower manufacturers to innovate and excel. With the right partner, such as the reputable professionals at deepmould.net, the potential of this technology can be fully realized, leading to remarkable advancements in product development and manufacturing efficiency.