Centrifugal Pumps: A Deep Dive into Functionality and Applications
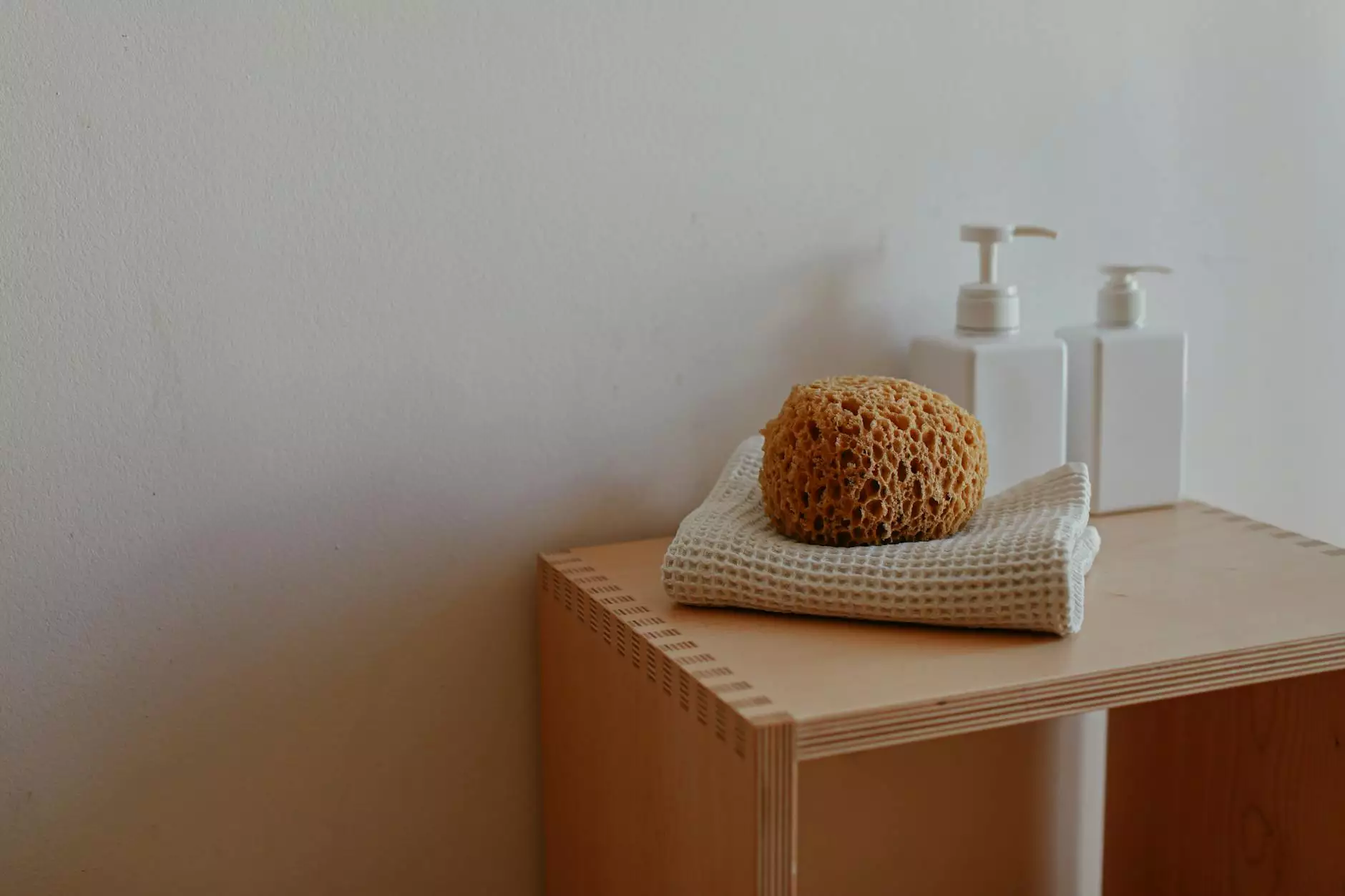
Centrifugal pumps are pivotal components in various industries, seamlessly transforming potential energy into kinetic energy to move fluids efficiently. Understanding their operation, maintenance, and applications can greatly benefit businesses that rely on fluid transportation. This article provides a comprehensive guide to centrifugal pumps, aiming to inform and educate readers on why they are indispensable in both industrial and agricultural settings.
1. What is a Centrifugal Pump?
A centrifugal pump is a mechanical device that uses rotational energy to move fluids. The heart of this pump is its impeller, which spins rapidly to create a centrifugal force, pushing the fluid outwards from the inlet and through the discharge outlet. This design makes centrifugal pumps exceptionally efficient for handling a variety of fluids, including water, chemicals, and slurries.
2. How Do Centrifugal Pumps Work?
The operation of a centrifugal pump can be broken down into several key phases:
- Fluid Entry: The pump is filled with fluid through the suction inlet.
- Impeller Action: As the impeller rotates, it converts the motor's mechanical energy into fluid energy. Fluid enters the impeller at the center (eye) and is flung outwards to the discharge.
- Pressure Increase: The movement of the fluid under centrifugal force creates a low-pressure area at the eye of the impeller, allowing more fluid to be drawn into the pump.
- Fluid Discharge: The fluid exits the pump at a higher pressure, driving it through the piping system.
This simple yet effective mechanism allows centrifugal pumps to operate efficiently in various applications, making them the most commonly used pumps worldwide.
3. Types of Centrifugal Pumps
Centrifugal pumps can be classified into different categories based on various criteria:
3.1 Based on the Impeller Design
- Open Impeller: Ideal for handling fluids containing solids.
- Closed Impeller: Provides higher efficiency and better hydraulic performance.
- Vortex Impeller: Suitable for handling liquids with a high concentration of solids or fibrous materials.
3.2 Based on Components
- Single-Stage Pumps: One impeller, common in low-pressure applications.
- Multi-Stage Pumps: Multiple impellers, designed for high-pressure applications.
3.3 Based on the Drive Mechanism
- Electric Motor Driven: Commonly used in industrial applications.
- Diesel Engine Driven: Often used in remote locations or where electricity is not available.
4. Applications of Centrifugal Pumps
The versatility of centrifugal pumps means they are widely used across various sectors:
4.1 Industrial Applications
In the industrial sector, centrifugal pumps play a crucial role in:
- Water Supply Systems: They manage water pressure in municipal systems.
- Pulp and Paper Industry: Used to transport pulp slurries.
- Chemical Processing: Critical for moving chemicals safely and efficiently.
4.2 Agricultural Sector
The agricultural industry heavily relies on centrifugal pumps for:
- Irrigation Systems: Ensuring that crops receive adequate water supply.
- Pesticide and Fertilizer Application: Facilitating the efficient distribution of essential nutrients.
4.3 HVAC Systems
Centrifugal pumps are integral to heating, ventilation, and air conditioning (HVAC) systems, where they are used to:
- Circulate Water: In heating and cooling processes.
- Maintain Environmental Control: By regulating temperatures and humidity.
5. Advantages of Using Centrifugal Pumps
Centrifugal pumps offer numerous benefits, making them a preferred choice for many applications:
- High Efficiency: Capable of handling large volumes of fluid with minimal energy consumption.
- Low Maintenance Cost: Their simple design translates to lower maintenance needs.
- Versatility: Able to pump a variety of fluids, from clean water to viscous chemicals.
- Durability: Constructed from robust materials that can withstand harsh operating conditions.
6. Maintenance and Troubleshooting of Centrifugal Pumps
To ensure the longevity and efficient performance of centrifugal pumps, regular maintenance is essential. Here are some key maintenance practices:
6.1 Regular Inspections
Conducting periodic inspections helps in identifying wear and tear early. Key areas to check include:
- Pumps for vibrations and unusual noises
- Seals and gaskets for leaks
- Bearings for signs of wear
6.2 Lubrication
Proper lubrication of bearings is crucial to prevent overheating and mechanical failure. Use lubricants recommended by the manufacturer.
6.3 Monitor Performance
Keep track of the pump’s performance metrics such as flow rate and pressure. Any significant deviation may indicate underlying issues.
7. Conclusion
In conclusion, centrifugal pumps are an essential part of modern industry and agriculture, offering unrivaled efficiency and versatility. Understanding their function, types, applications, and maintenance is vital for any business that relies on fluid movement. Whether it’s for agricultural irrigation, HVAC systems, or chemical processing, the right centrifugal pump can significantly enhance operational efficiency and reliability.
For businesses like Michael Smith Engineers, specializing in services such as auto repair, farm equipment repair, and structural engineering, mastering the use of centrifugal pumps can lead to improved service offerings and customer satisfaction. Investing in quality centrifugal pumps and understanding their mechanics can provide unprecedented advantages in today’s competitive market.