CNC Turning Parts Factory: Revolutionizing Metal Fabrication
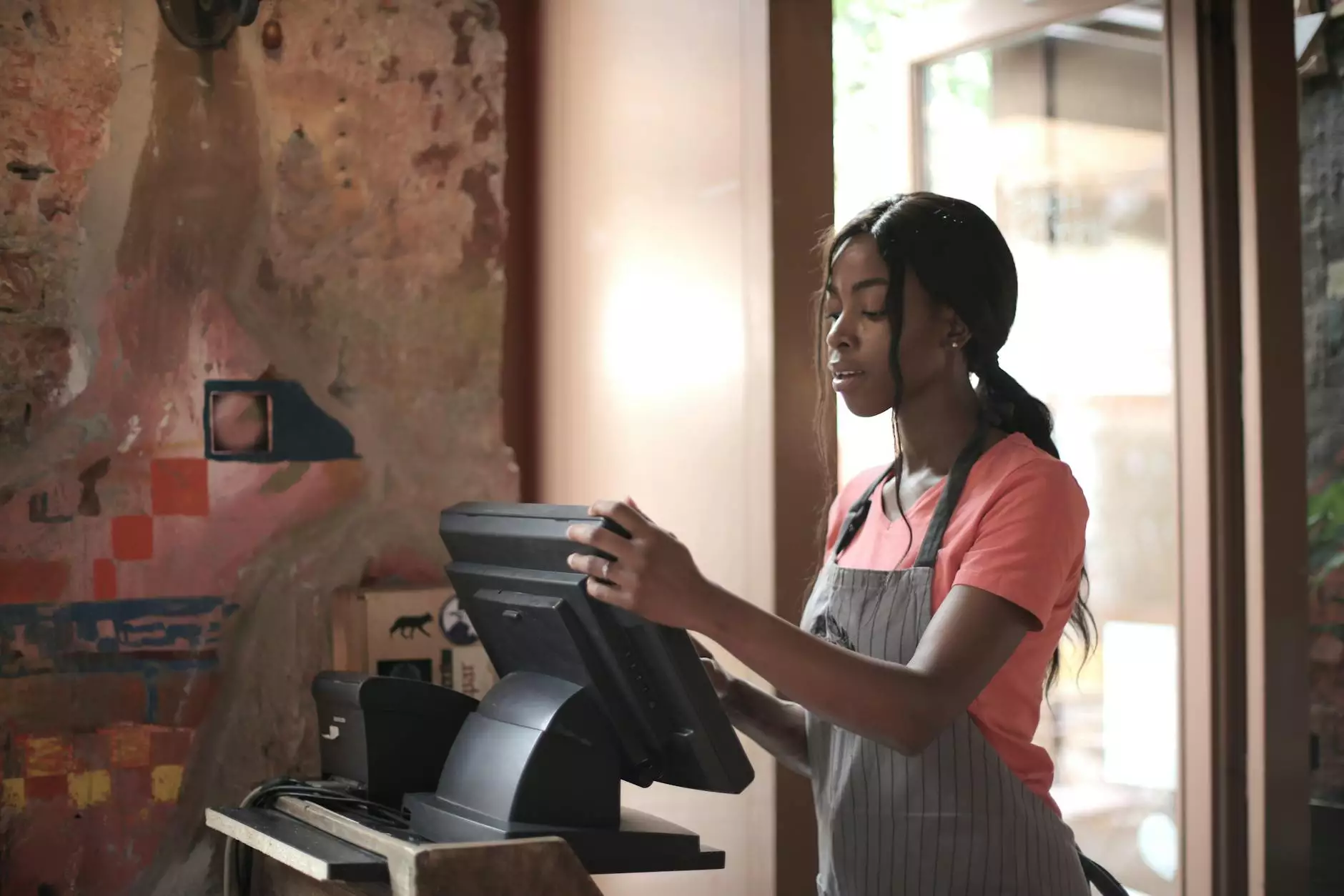
The journey of modern manufacturing begins at the CNC turning parts factory, where advanced technologies meet skilled craftsmanship to produce precision-engineered components. This article delves into the intricate workings of CNC turning processes, their applications in various industries, and the undeniable benefits of utilizing such factories for achieving top-notch metal fabrication.
What is CNC Turning?
CNC turning is a computer-numerical control (CNC) process that involves rotating a workpiece while a cutting tool shapes it into desired dimensions. This method is pivotal in producing cylindrical parts with high accuracy and repeatability. The capabilities of a CNC turning parts factory extend far beyond traditional machining, as it incorporates automation, allowing for greater efficiency and reduced human error.
The Process of CNC Turning
The CNC turning process involves several key stages:
- Design and Programming: The first step involves designing the part using CAD software. The design is then translated into a CNC program that guides the machine's operations.
- Material Selection: Common materials used in CNC turning include metals such as steel, aluminum, and brass, but plastics and composites are also viable options.
- Setup: The workpiece is securely mounted on the lathe, and the tooling is prepared for the machining operations.
- Machining: During the turning operation, the CNC machine rotates the material while the tool cuts it to achieve the desired shape and size.
- Finishing: After turning, parts may undergo additional operations such as sanding, polishing, or coating to meet tight tolerances and surface finish requirements.
Advantages of CNC Turning Parts Factories
When considering a CNC turning parts factory for your manufacturing needs, several benefits stand out:
- Precision and Accuracy: CNC turning machines are designed to achieve incredibly tight tolerances, ensuring a level of precision that is unmatched by manual machining.
- Consistency: Automated processes allow for the consistent production of parts, making it easier to maintain quality across large production runs.
- Cost-Effectiveness: Although the initial setup cost can be high, CNC turning leads to lower production costs over time due to reduced labor and increased efficiency.
- Versatility: CNC turning can accommodate a wide range of materials and complex designs, making it suitable for various applications.
- Reduced Waste: The precision of CNC turning minimizes material waste, as parts can be machined more efficiently than traditional methods.
Applications of CNC Turning in Various Industries
The applications of CNC turning are vast, spanning multiple industries. Here are some notable examples:
Aerospace Industry
In the aerospace sector, where safety and precision are paramount, CNC turning is used to create components such as:
- Engine parts
- Landing gear components
- Brackets and housings
The stringent quality standards in aerospace manufacturing make CNC turning an ideal choice for producing critical components.
Automotive Sector
The automotive industry relies heavily on CNC turning for the production of:
- Axles
- Drive shafts
- Transmission parts
CNC turning enables manufacturers to produce complex parts that meet the high-performance requirements of modern vehicles.
Medical Devices
In the medical field, precision is essential. CNC turning is utilized for creating:
- Implants
- Instrumentation
- Customized surgical tools
The ability to produce sterile and precise components is crucial in medical applications, where accuracy can impact patient outcomes.
Electronics and Telecommunications
The fast-paced world of electronics demands parts that are both lightweight and durable. CNC turning supplies parts such as:
- Connectors
- Enclosures
- Heat sinks
These components are integral to the functionality of various electronic devices, making CNC turning indispensable in the tech landscape.
Choosing the Right CNC Turning Parts Factory
Finding the right CNC turning parts factory is crucial for ensuring quality and reliability. Here are some factors to consider when making your choice:
Experience and Expertise
Look for a factory with a proven track record in CNC turning. Experienced manufacturers will have the technical knowledge and expertise needed to produce high-quality parts efficiently.
Quality Certifications
Ensure that the factory adheres to international quality standards such as ISO 9001. Certifications indicate a commitment to maintaining quality and consistency across all manufacturing processes.
Technology and Equipment
Examine the technology and equipment used in the factory. Advanced CNC machines equipped with the latest software and tools will lead to more efficient production and better-quality parts.
Customer Service
A reliable CNC turning parts factory should offer excellent customer service. Communication is vital, from initial consultations through to post-production support.
Conclusion
In conclusion, the CNC turning parts factory plays a crucial role in modern manufacturing across various industries. From aerospace and automotive to medical and electronics, the advantages of CNC turning are profound. The ability to produce high-precision components with consistent quality significantly enhances production capabilities and drives innovation.
As you explore your manufacturing options, consider partnering with a reputable factory like deepmould.net that specializes in metal fabrication and can cater to your specific CNC turning needs. The future of manufacturing is here, and CNC turning is at its forefront.